Understanding Die Casting Products: Transforming Industries
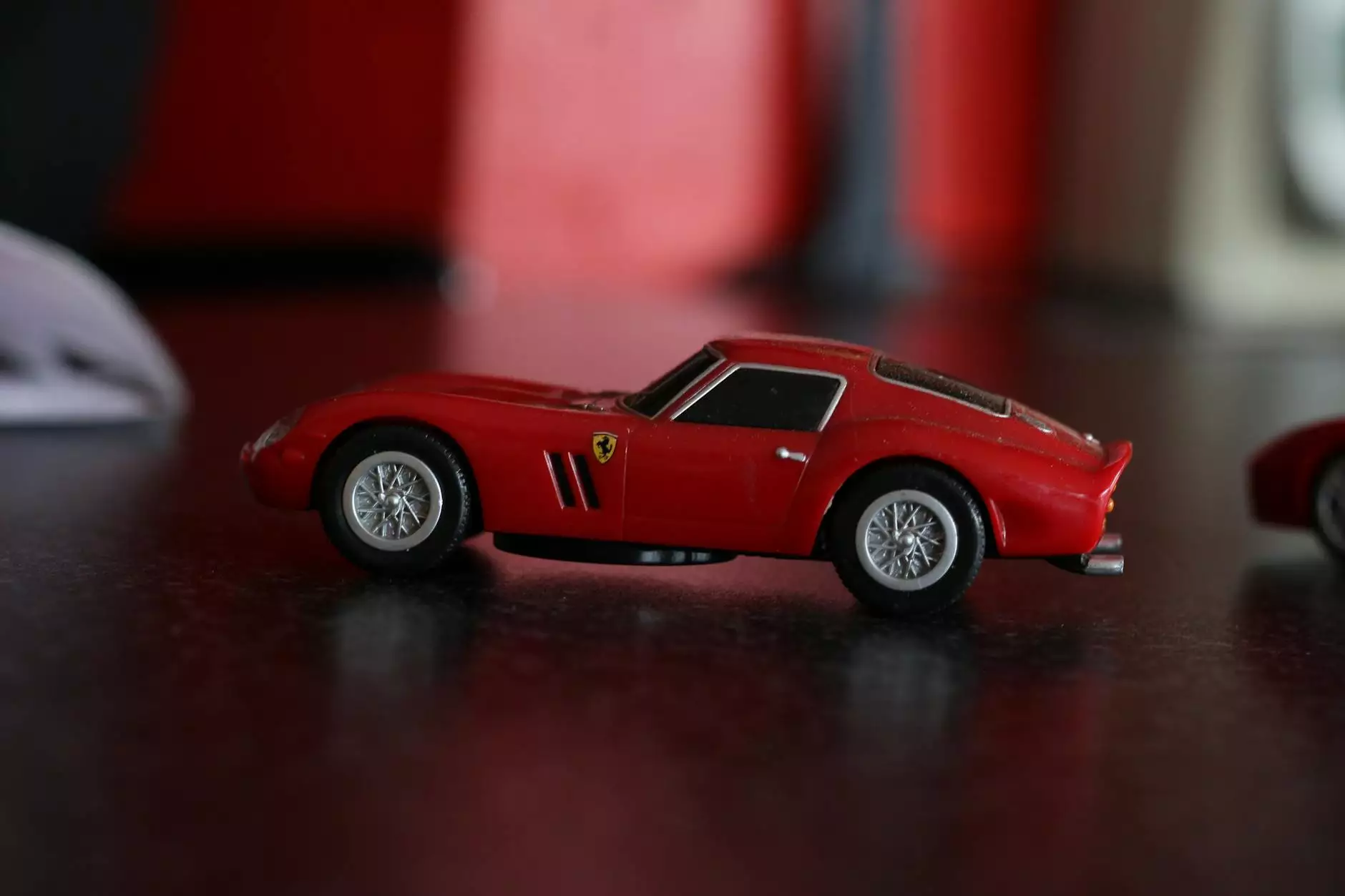
Die casting products are essential components in various industries, ranging from automotive to electronics. These products are created through a manufacturing process that involves pouring molten metal into a mold, allowing for the creation of highly accurate and intricate designs. This article aims to delve deep into the die casting process, its advantages, applications, and the critical role it plays in modern manufacturing.
What is Die Casting?
Die casting is a highly efficient manufacturing process used to produce die casting products made from non-ferrous metals such as aluminum, zinc, and magnesium. The process involves the following key steps:
- Preparation: The metal is melted in a furnace.
- Injection: The molten metal is injected into a steel mold under high pressure.
- Cooling: Once the metal fills the mold, it is allowed to cool and solidify.
- Removal: The die is opened, and the finished product is ejected.
The Advantages of Die Casting Products
Die casting offers numerous benefits over other manufacturing techniques, making it a preferred choice in many applications:
- High Precision: Die casting allows for high tolerances, ensuring that products fit together perfectly.
- Cost Efficiency: Thanks to its speed, die casting reduces labor and material costs, making it economically viable for large production runs.
- Versatility: It can produce complex shapes and designs, allowing for creativity in product development.
- Durability: The products manufactured are robust, with excellent structural integrity.
Applications of Die Casting Products
Die casting products are integral to various sectors, each benefiting from the unique properties of die casting:
1. Automotive Industry
The automotive industry is one of the largest consumers of die casting products. Components such as engine blocks, transmission cases, and decorative parts are commonly produced using this method. The durability and lightweight nature of aluminum die casting make it particularly valuable for enhancing fuel efficiency.
2. Electronics
In electronics, die casting products are used to create housings for devices and other component parts that require precise dimensional control. The aesthetic appeal and finish further enhance the product's market value.
3. Industrial Equipment
Many industrial machines consist of die cast components because they require strength alongside lightweight properties. Products like gear housings and structural components are commonly made through die casting.
The Die Casting Process Explained
Having briefly discussed the die casting process, let’s examine it in detail:
1. Metal Melting
The process begins with melting the selected metal alloy. Typically, aluminum and zinc are favored due to their excellent casting properties. This molten metal must reach a specific temperature, usually between 700°C and 800°C, before it can be injected into the die.
2. Die Injection
Once the metal is molten, it is injected into a pre-heated die at high pressure, often exceeding 10,000 psi. This pressure ensures that the metal fills every crevice of the mold, which is essential for producing detailed designs.
3. Cooling and Solidification
After injection, the die remains closed for a predetermined period, allowing the metal to cool and solidify. Cooling times can vary based on the size and shape of the part being produced.
4. ejection and Finishing
Once the part has solidified, the die opens, and the finished product is ejected. Additional finishing processes such as machining, plating, or painting may occur to enhance the final product's appearance and performance.
Choosing the Right Die Casting Service Provider
When selecting a manufacturer for die casting products, consider the following factors:
- Experience and Expertise: Look for providers with a proven track record in die casting.
- Technology: Advanced manufacturing technology can significantly affect the quality of the final product.
- Quality Control: Ensure they have robust quality control processes to maintain consistency and precision.
- Design Capabilities: A manufacturer should offer design assistance to optimize product performance and manufacturability.
The Future of Die Casting Products
The future of die casting products looks bright, driven by innovation and advancements in technology. Here are some trends to watch:
1. Sustainable Practices
With increasing environmental awareness, die casting companies are adopting sustainable practices, such as recycling materials and reducing energy consumption during the production process. This not only benefits the planet but also reduces costs associated with waste disposal.
2. Advances in Materials
New aluminum and zinc alloys are being developed to enhance the strength and performance of die casting products. These innovations will allow manufacturers to create even lighter and more robust components.
3. Increased Automation
Automation in die casting processes is on the rise, leading to higher production rates and less human error. Robotic arms and automated systems can streamline the production line, allowing for faster turnaround times and improved quality.
Conclusion
In conclusion, die casting products play a pivotal role in numerous industries, thanks to their precision, durability, and cost-effectiveness. Understanding the die casting process and its benefits can help businesses make informed decisions about their manufacturing needs. As technology continues to evolve, die casting will remain a cornerstone of modern industry, offering innovative solutions that meet the demands of the future.
For those seeking high-quality die casting products, DeepMould.net offers an extensive range of solutions tailored to your business’s unique needs. Partnering with experienced metal fabricators not only ensures exceptional product quality but also fosters growth and sustainability in your operations.
Explore the transformative potential of die casting products with DeepMould today!