Understanding Tooling Die Casting in Metal Fabrication
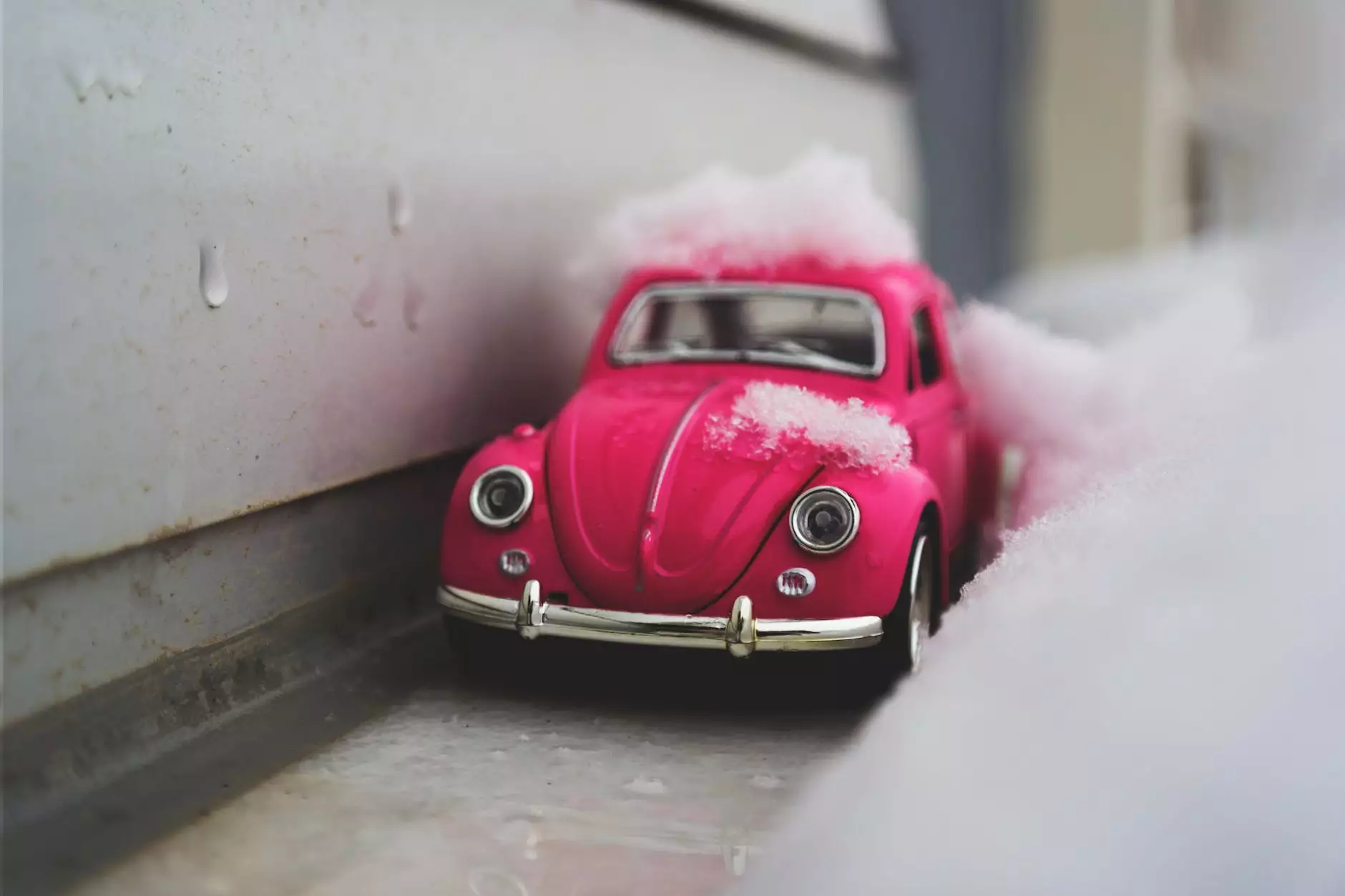
In the competitive landscape of manufacturing, tooling die casting stands out as a pivotal technique that brings precision and efficiency to metal fabrication processes. This comprehensive guide will delve into the essentials of tooling die casting, exploring its benefits, processes, and the technological advancements that make it indispensable in modern manufacturing.
What is Tooling Die Casting?
Tooling die casting refers to a manufacturing process that involves pouring molten metal into a specially designed mold to produce precise and intricate parts. This method is widely used in various industries, including automotive, aerospace, and consumer products. By using a metal die, manufacturers can create components with complex geometries and superior surface finishes with high repeatability and minimal waste.
The Die Casting Process Explained
The process of tooling die casting consists of several key stages. Understanding these stages is crucial for appreciating its efficiency and applications:
1. Design Phase
- Pencil to Pixel: The first phase is the design of the part, which involves creating detailed CAD drawings that outline the dimensions, tolerances, and features of the final product.
- Prototype Development: Building a prototype helps in testing the design and making necessary adjustments before committing to full-scale production.
2. Tooling Construction
- Creating the Die: The die, which serves as the mold, is created using high-quality steel to withstand the immense pressure and temperature during production.
- Precision Engineering: Advanced machining techniques ensure that the die accurately reflects the design specifications.
3. Melting and Injection
- Metal Melting: The metal, typically aluminum, zinc, or magnesium, is melted in a furnace until it reaches a liquid state.
- Injection into the Die: Once molten, the metal is injected into the die under high pressure to fill the mold completely within a fraction of a second.
4. Cooling and Ejection
- Cooling Phase: The molten metal is allowed to cool and solidify within the die, forming the desired part.
- Ejection: Once cooled, the die opens, and the finished part is ejected, ready for further processing or finishing.
Benefits of Tooling Die Casting
The advantages of using tooling die casting in metal fabrication are numerous:
- Cost Efficiency: Mass production leads to reduced costs per unit, making it a preferred method for high-volume manufacturing.
- High Precision: Die casting produces components with extreme accuracy and detail, minimizing the need for additional machining.
- Complex Geometries: The ability to create intricate shapes allows for innovations in product design.
- Superior Surface Finish: Parts produced through this process typically exhibit excellent surface qualities, reducing the need for secondary finishing processes.
- Material Versatility: Various alloys can be used, enabling manufacturers to choose the right material for their specific application.
Applications of Tooling Die Casting
Due to its many benefits, tooling die casting finds applications across numerous industries:
- Automotive Industry: Engine parts, transmission housings, and structural components.
- Aerospace: Components such as brackets, housings, and structural parts that require lightweight and durable materials.
- Consumer Electronics: Cases, frames, and other parts that require intricate designs and high-quality finishes.
- Medical Devices: Critical components that require stringent quality and precision standards.
Choosing the Right Partner for Tooling Die Casting
When it comes to tooling die casting, selecting the right manufacturing partner is crucial for ensuring quality and efficiency. At deepmould.net, we pride ourselves on our expertise in metal fabrication, offering comprehensive die casting solutions tailored to your specific needs.
Why Choose Deep Mould?
- Expertise: Our team of professionals has extensive experience in tooling die casting and can guide you through every step of the process.
- Advanced Technology: We utilize state-of-the-art technology and equipment to ensure that every component produced meets the highest standards.
- Quality Assurance: Our rigorous quality control processes ensure that every product exceeds your expectations.
- Customer Support: We prioritize customer satisfaction, providing dedicated support from design to delivery.
The Future of Tooling Die Casting
The future of tooling die casting is bright, thanks to ongoing advancements in technology and manufacturing processes. The integration of smart manufacturing practices, including the Internet of Things (IoT) and automation, is set to revolutionize the industry.
Innovation Trends
- 3D Printing Technology: The emergence of 3D printing is changing how dies are produced, allowing for rapid prototyping and reduced lead times.
- Environmentally Friendly Practices: Manufacturers are increasingly focusing on sustainable practices, including recycling scrap materials and reducing energy consumption.
- Data Analytics: Leveraging data to monitor processes will enhance quality control and operational efficiency, ensuring that manufacturing is both fast and cost-effective.
Conclusion
In summary, tooling die casting is an essential component of modern metal fabricators' toolbox, offering unmatched precision and efficiency. Whether you are in the automotive, aerospace, or consumer goods sector, the advantages of adopting this technique can lead to significant benefits in your manufacturing processes. Partnering with experienced professionals like deepmould.net ensures that you can leverage the full potential of tooling die casting to meet your business needs, enhance product quality, and drive innovation.
As the manufacturing landscape continues to evolve, staying abreast of the latest advancements and trends in tooling die casting will be crucial for maintaining competitiveness and achieving success.