The Importance of Quality Cylinder Liner Manufacturing
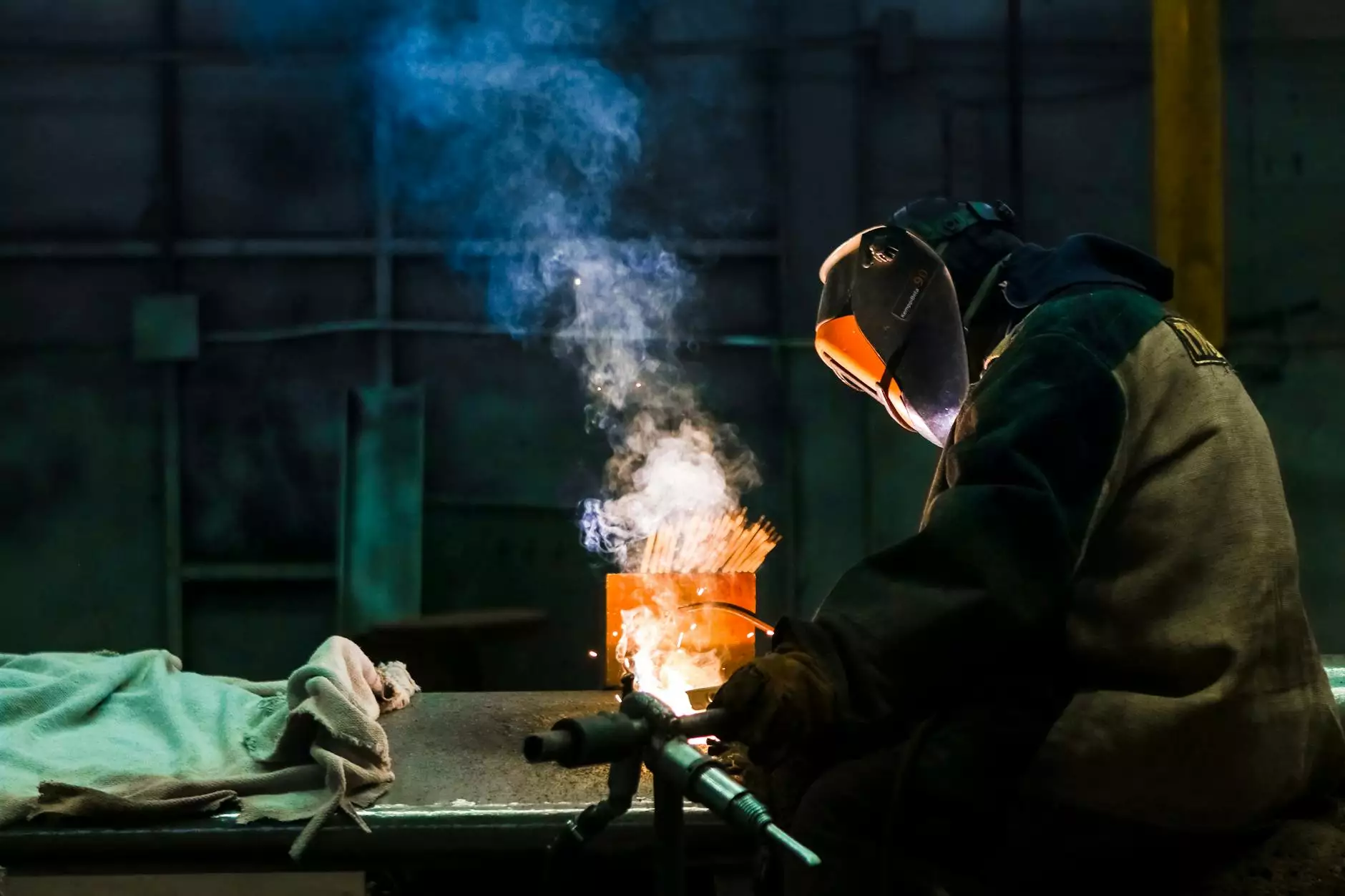
As a prominent cylinder liner manufacturer, we recognize the pivotal role that cylinder liners play in the performance and longevity of diesel engines. At client-diesel.com, we are dedicated to providing exceptional quality and precision in every product we deliver. This article explores in-depth the intricacies of cylinder liner manufacturing, the significance of high-quality components in diesel engine performance, and how our products stand out in the competitive market.
Understanding Cylinder Liners
Cylinder liners are critical components in diesel engines. They serve as a protective barrier between the combustion gases and the engine block while also facilitating the movement of pistons. Understanding the types and materials of cylinder liners is essential for proper engine maintenance and performance.
- Types of Cylinder Liners:
- Dry Liners: These liners do not come in contact with coolant and are primarily used in high-performance engines.
- Wet Liners: These are surrounded by coolant, helping in temperature management in engines.
- Materials Used:
- Cast Iron: Known for its durability and strength, cast iron is commonly used in manufacturing cylinder liners.
- Aluminum: Lightweight and excellent at heat dissipation, aluminum is increasingly popular for high-performance applications.
The Manufacturing Process of Cylinder Liners
The manufacturing of cylinder liners is a multi-step process that requires precision engineering and high-quality materials. Below are the essential stages of the process:
1. Material Selection
The first step in manufacturing cylinder liners is selecting the right material, which determines the durability and performance characteristics of the liners. At client-diesel.com, we source only the best materials tailored to the specific demands of our clients’ engines.
2. Casting
Using advanced casting techniques, we shape the selected raw materials into the initial form of the cylinder liner. This process is vital as it sets the foundation for strength, durability, and heat resistance.
3. Machining
After casting, the liners undergo precision machining. This includes boring, honing, and finishing operations to ensure the liners meet exacting tolerances necessary for effective engine performance.
4. Surface Treatment
To enhance the durability of the cylinder liners, surface treatments such as hardening and coating are applied. These treatments improve wear resistance and reduce friction during engine operation.
5. Quality Control
Quality assurance is crucial in cylinder liner manufacturing. Our rigorous testing procedures include dimensional checks, material inspections, and performance assessments to guarantee that each cylinder liner meets industry standards and client expectations.
Why Quality Matters in Cylinder Liner Manufacturing
The quality of the cylinder liners has a direct impact on the performance and longevity of diesel engines. Poorly manufactured liners can lead to various issues, including:
- Reduced Engine Efficiency: Inadequate seal or improper dimensions can decrease engine efficiency.
- Increased Wear and Tear: Substandard liners degrade faster, resulting in increased maintenance costs and reduced engine lifespan.
- Overheating: Liners that do not dissipate heat effectively can contribute to engine overheating, which can cause catastrophic failures.
By choosing a reputable cylinder liner manufacturer like client-diesel.com, you ensure that your diesel engines operate at peak performance and are less prone to issues over time.
Customer-Centric Approach to Cylinder Liner Manufacturing
At client-diesel.com, our commitment to customer satisfaction drives every aspect of our cylinder liner production. We understand that each client's needs are unique, and we tailor our solutions accordingly. Here’s how we foster a customer-centric approach:
1. Custom Solutions
We offer customized cylinder liners designed to meet the specific requirements of various engine models. Our team of experts works closely with clients to understand their needs and provide tailored products.
2. Advanced Technology
Utilizing cutting-edge technology in our manufacturing processes allows us to produce high-precision cylinder liners that not only meet but exceed industry standards.
3. Exceptional Customer Support
Our dedicated customer support team is always available to assist with inquiries, provide technical support, and guide clients through the selection process.
The Competitive Edge of Client-Diesel
As a leading cylinder liner manufacturer, client-diesel.com has established a strong reputation for reliability and innovation in the industry. Here are some of the advantages of partnering with us:
- Extensive Industry Experience: With years of experience, we have developed a deep understanding of the cylinder liner market and the needs of our customers.
- Innovative Practices: We continually invest in research and development to improve our manufacturing processes and product offerings.
- Sustainable Practices: Our commitment to sustainability ensures that our manufacturing processes are environmentally friendly, without compromising on quality.
The Future of Cylinder Liners in Diesel Engines
As technology advances, the demands on diesel engines evolve, resulting in the need for better-designed components. The future of cylinder liner manufacturing is poised for significant developments:
- Enhanced Materials: Research into new composite materials that provide superior strength and thermal resistance is on the rise.
- Smart Technology Integration: With the advent of IoT and smart manufacturing, we expect to see more advanced monitoring systems integrated into cylinder liners for predictive maintenance.
- Focus on Fuel Efficiency: As the pressure increases to reduce emissions, cylinder liners will play a crucial role in improving fuel efficiency and overall engine performance.
Conclusion
In the realm of diesel engines, the importance of high-quality cylinder liners cannot be overstated. As a dedicated cylinder liner manufacturer, client-diesel.com stands at the forefront of this industry, committed to delivering excellence in every product we produce. From our rigorous manufacturing processes to our customer-centered approach, we ensure that our clients receive the best solutions tailored to their needs.
The future of cylinder liner manufacturing is bright, and we are excited to lead the way in innovation, quality, and customer satisfaction.