Insulated Concrete Forms Building Plans: The Future of Sustainable Construction
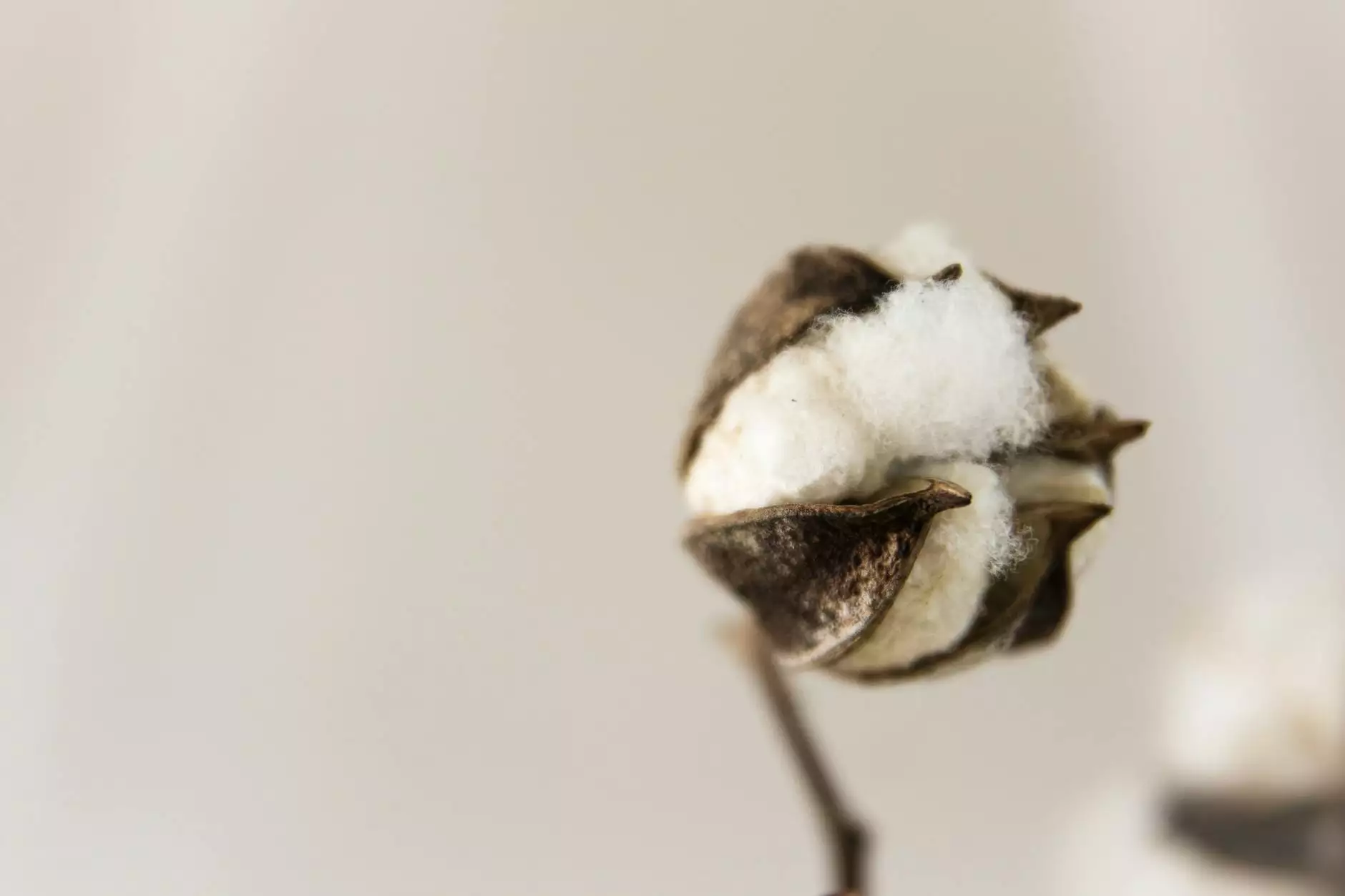
Insulated concrete forms (ICFs) are rapidly transforming the landscape of modern construction, providing builders and homeowners with innovative solutions that prioritize energy efficiency, sustainability, and structural integrity. This article will delve deep into the advantages of ICF building plans, best practices for implementation, and why they might be the right choice for your next construction project.
What are Insulated Concrete Forms?
Insulated concrete forms are thick, foam blocks that serve as both insulation and mold for pouring concrete. When the concrete sets, it creates a solid, energy-efficient structure that can be used in various applications, from residential homes to commercial buildings. ICFs have gained immense popularity due to their ability to provide excellent thermal performance, sound insulation, and superior resistance to natural disasters.
The Benefits of Using Insulated Concrete Forms
1. Energy Efficiency
One of the paramount benefits of using insulated concrete forms building plans is their remarkable energy efficiency. ICF structures typically have an R-value ranging from 20 to 40, which significantly surpasses traditional wood-frame construction. This high insulation value means that homes built with ICFs require less energy for heating and cooling, leading to lower utility bills and a decreased carbon footprint.
2. Durability and Longevity
Buildings constructed with ICF technology are exceptionally durable. The use of concrete provides a structure that is resistant to damage from pests, such as termites, and is better at withstanding severe weather conditions, including hurricanes and earthquakes. This longevity not only protects your investment but also enhances the safety and comfort of your living or working environment.
3. Soundproofing Qualities
Another advantage of using insulated concrete forms is their superior soundproofing capabilities. The combination of concrete and foam insulation creates a barrier that minimizes noise pollution, making ICF structures an ideal choice for residential areas, schools, and offices situated in bustling environments.
4. Environmental Sustainability
ICFs contribute to sustainable building practices by utilizing materials that are recyclable and by enhancing energy efficiency. The reduced energy consumption of ICF buildings translates to lower greenhouse gas emissions. Building with ICFs also promotes a healthier indoor environment by minimizing air leakage and controlling moisture levels, which can be crucial for maintaining good indoor air quality.
Design Flexibility with Insulated Concrete Forms
Contrary to what some may believe, insulated concrete forms offer extensive design flexibility. They can be utilized for complex architectural designs, allowing for creativity in both residential and commercial projects. Whether it’s a sleek modern home or a traditional-style building, ICFs can adapt to a variety of aesthetic visions while maintaining structural integrity.
How to Implement ICF Building Plans
1. Planning and Design
Before embarking on your construction journey with insulated concrete forms, it’s essential to work with an experienced architect or builder who understands ICF technology. They can guide you in developing insulated concrete forms building plans that meet your specific needs while adhering to local building codes and regulations. Your design should consider factors such as:
- Building orientation for optimal energy efficiency.
- Window and door placements for maximum natural light.
- Roof designs that complement the ICF walls.
2. Foundation and Site Preparation
Just like traditional building methods, site preparation for ICF construction is crucial. This involves clearing the land, grading the site, and laying a proper foundation. ICFs can be used with a variety of foundation types, including slab, crawl space, or basement foundations. It’s essential to ensure that the foundation is compatible with the ICF system chosen.
3. Assembly and Construction
The assembly of ICFs is typically faster than conventional construction methods. The blocks interlock easily, allowing for quicker installation. Moreover, the need for framing is reduced since the forms themselves provide structural support. Skilled labor is still required to ensure the concrete is poured and set correctly, avoiding common pitfalls such as voids or uneven surfaces.
Cost Considerations of ICF Construction
While the initial cost of insulated concrete forms can be higher than traditional building materials, the long-term savings in energy costs and maintenance can justify the investment. It’s essential to consider the total cost of ownership when evaluating ICFs. Over time, the ROI becomes evident through lower heating and cooling bills, reduced insurance premiums due to the increased durability, and sometimes even tax incentives for environmentally friendly building practices.
Conclusion: The Future is Here with Insulated Concrete Forms
As the construction industry continues to evolve, the adaptation of new technologies and materials like insulated concrete forms signifies a turn towards smarter and more sustainable building practices. For builders, architects, and homeowners, embracing ICF technology represents a step towards higher efficiency, durability, and design freedom.
When planning your next building project, consider exploring insulated concrete forms building plans. Investing in energy-efficient, sustainable materials will not only benefit your immediate project but contribute to a healthier planet for future generations. Embrace the future of construction and discover the countless advantages of ICFs with Fry Design Co., where innovative design meets sustainability!