The Essential Role of an Automotive Mold Manufacturer
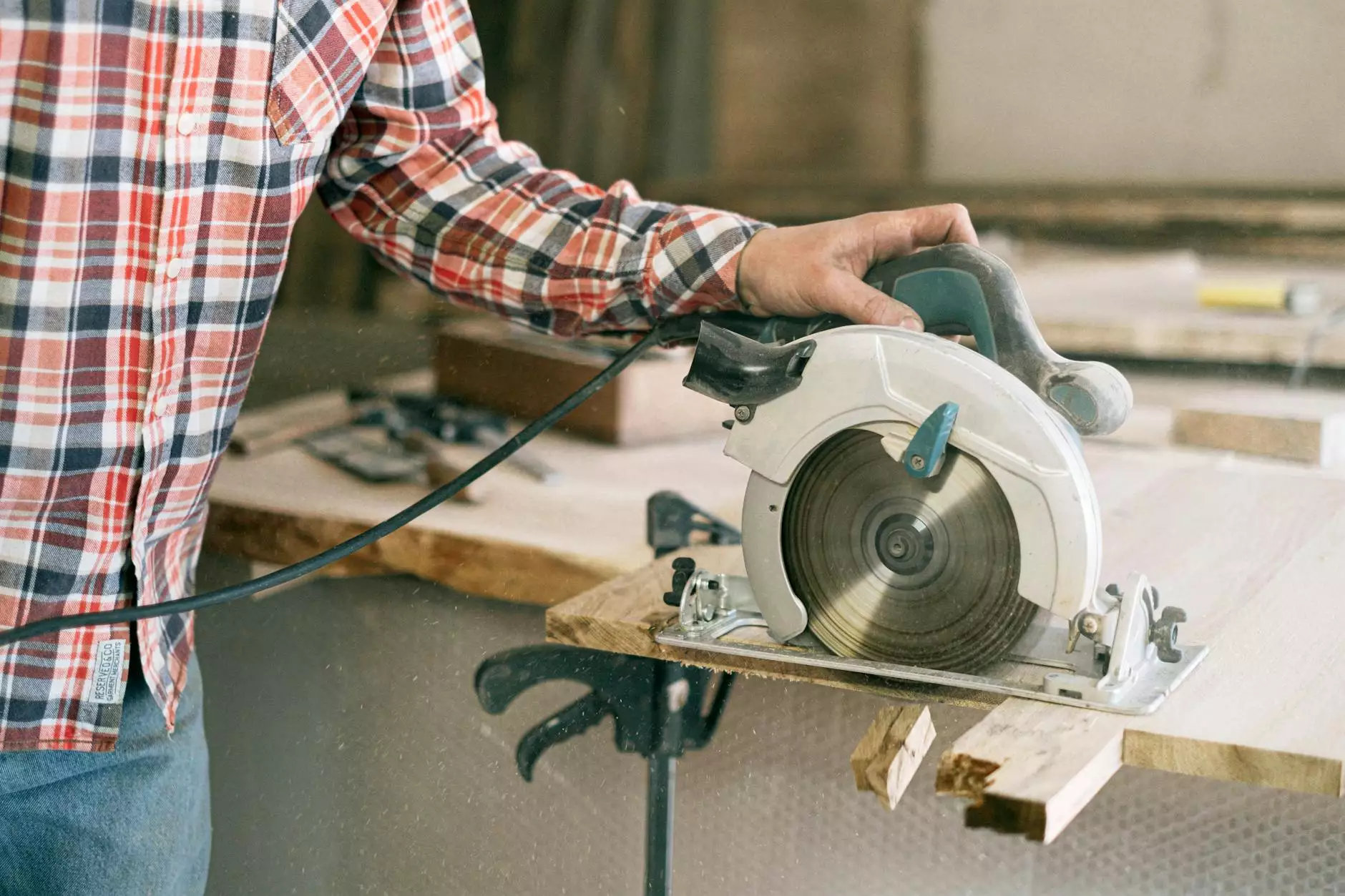
In today’s fast-paced automotive industry, where efficiency and precision are paramount, the role of an automotive mold manufacturer cannot be overstated. Automotive molds are critical components in the production of various parts, embodying the blend of advanced manufacturing techniques and innovative design.
Understanding the Basics of Automotive Molds
Automotive molds are specialized tools used to shape materials into specific designs, yielding high-precision parts that meet stringent industry standards. These molds are created from metals such as steel or aluminum and are designed to withstand high pressure and temperatures during the production process.
The Importance of Automotive Mold Manufacturing
The significance of an automotive mold manufacturer extends beyond mere production. Here are some vital aspects that underline this importance:
- Precision Engineering: The automotive industry demands parts that fit together perfectly. Molds manufactured to high precision ensure that components maintain tight tolerances, which is critical for vehicle safety and performance.
- Cost-Effectiveness: By using advanced manufacturing techniques, automotive molds can be produced with optimal material efficiency, reducing waste and lowering production costs over time.
- Scalability: Experienced automotive mold manufacturers can scale up production quickly to meet market demands, ensuring that manufacturers can respond to changes without compromising quality.
- Innovation Facilitation: The automotive industry is rapidly evolving with new technologies such as electric vehicles and autonomous driving. A competent mold manufacturer is pivotal in integrating new materials and designs into production processes, supporting innovation.
Key Processes in Automotive Mold Manufacturing
The process of manufacturing automotive molds involves several critical steps that ensure the final product meets rigorous standards. Below are the typical stages of mold manufacturing:
- Design Phase: Initially, advanced software tools are utilized to design the mold. Using CAD (Computer-Aided Design) systems helps engineers create detailed mold designs, enabling precise modeling of the end product.
- Material Selection: Selecting the right material is essential for durability and performance. Steel is commonly used for high-volume production molds, while aluminum may be selected for low-volume applications due to its lighter weight and lower costs.
- Machining: After the design is approved, the actual machining process begins. This involves cutting and shaping the mold using CNC machines to achieve the utmost precision.
- Finishing: Once the primary machining is complete, molds undergo finishing processes such as polishing and coating to enhance surface quality and reduce friction during the molding operation.
- Testing: Finally, molds are rigorously tested to ensure that they meet the specified quality standards before being deployed for production.
Innovations in Automotive Mold Manufacturing
As the automotive industry integrates more advanced technology, automotive mold manufacturers like Deep Mould are at the forefront of innovation. Some recent trends in the field include:
- 3D Printing: Rapid prototyping through 3D printing significantly reduces development time and costs. It allows manufacturers to quickly test designs and make necessary adjustments before the final mold production.
- Smart Manufacturing: Incorporation of IoT (Internet of Things) technology in the manufacturing process enables real-time monitoring and optimization of mold operations, leading to improved efficiency and reduced cycle times.
- Sustainable Practices: Increasing environmental consciousness has driven manufacturers to adopt sustainable practices, including recycling materials and reducing energy usage during the manufacturing process.
Choosing the Right Automotive Mold Manufacturer
Selecting a reliable automotive mold manufacturer is crucial for the success of any automotive production company. Here are several factors to consider when making this decision:
- Experience and Reputation: It is critical to choose a manufacturer with a proven track record in the industry, signifying that they can deliver high-quality products consistently.
- Capability and Capacity: Ensure that the manufacturer has the technical capabilities and capacity to meet your specific production needs, including volume and timelines.
- Technology Utilization: A manufacturer that employs the latest technology and techniques will usually produce higher quality molds and parts.
- Support and Communication: Effective communication throughout the manufacturing process is essential. Choose a company that offers excellent customer support and transparency.
The Future of Automotive Mold Manufacturing
As the automotive industry braces for technological disruptions and shifts toward electrification and automation, the future of automotive mold manufacturing looks promising yet challenging. With new materials being experimented with, such as thermoplastics and bio-materials, manufacturers will need to adapt their processes to accommodate these changes.
Additionally, environmental regulations will continue to shape manufacturing practices, pushing companies towards greener methodologies. Those who embrace these changes, like Deep Mould, will not only increase their competitiveness but also contribute positively to the planet.
Conclusion
In conclusion, the role of an automotive mold manufacturer is indispensable in the automotive industry. By ensuring precision, efficiency, and innovation, these manufacturers are key to the successful production of high-quality automotive components. As this industry evolves, the need for skilled manufacturers who are committed to excellence is greater than ever.
If you are looking for a partner in automotive mold manufacturing, consider exploring what Deep Mould has to offer. Their extensive expertise in metal fabrication ensures that they are well-equipped to handle the unique needs of today's automotive manufacturers, combining quality, cost-effectiveness, and advanced technology in every project.